Optimising the Aerodynamic drag of an Olympic Athlete - Sports Equipment System
- kristan209
- Feb 18, 2022
- 3 min read
Updated: Sep 8, 2022
“Our experience in pushing performance boundaries and developing athlete performance spans over a 27 year period, bringing together expertise from the aerospace, F1 Motorsport and Academic sectors.”
We have supported numerous athletes between Salt Lake City 2002 and Beijing 2022 to win World and Olympic medals, push personal bests including: #kimberleybos NED, #domparsons GBR, #alexhanssen NOR, #shelleyrudman GBR, #kristanbromley GBR, #alexcoomber GBR.
We have worked as a performance technology service provider to the Dutch Sliding Association BSBN, Olympic Team NL, Norwegian Olympic Skeleton Team, Team GB, UK Sport.
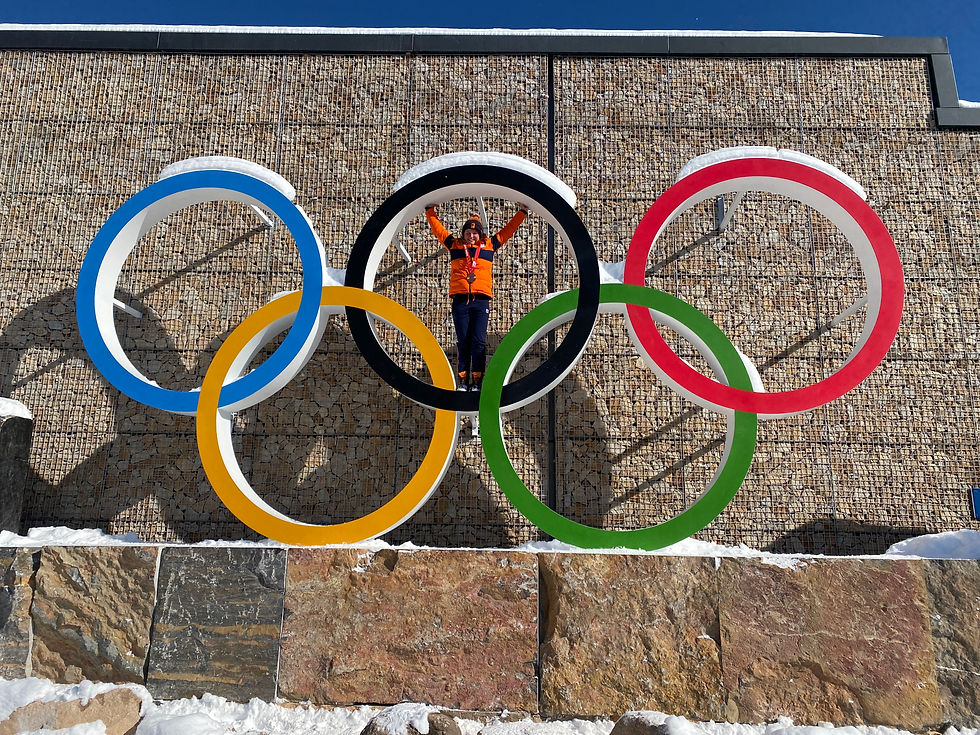
2022 World Number One & Olympic Medallists Kimberley Bos celebrating in Beijing 2022
The Challenge:
The ongoing quad cycle challenge is to reduce the aerodynamic drag of a Skeleton athlete system in support of medal success in a target competition.
Background:
The wind resistance that slows a Skeleton athlete's performance is a complex system that is influenced by multiple factors:
Athlete geometry
Sled design
Helmet design
Apparel design
Research shows that small changes in these factors can influence the overall aerodynamic drag of the athlete down 1 mile of ice at speeds of up to 140km/hr. Design innovations that can create drag reductions are sought after by all teams and are the focus of considerable R&D works.
“1/3 of the energy of an athlete travelling down an ice track is lost to wind resistance..”
Video of 2022 World Number One Kimberley Bos NED in action during training an the 2022 Beijing Olympic Yanqing Sliding Centre. The close proximity of the athlete/sled to the ice at speeds up to 140km/hr and the changing track geometry during the run results in complex aerodynamic system
Our Solution
Creating a Digital Twin
The first step is to create a digital twin of the athlete system. This involves 3d scanning and reverse engineering of the athlete's form including race wear (helmet/suit/sprint shoes) and combining this with sled design CAD data to create a full digital model of the athlete system.
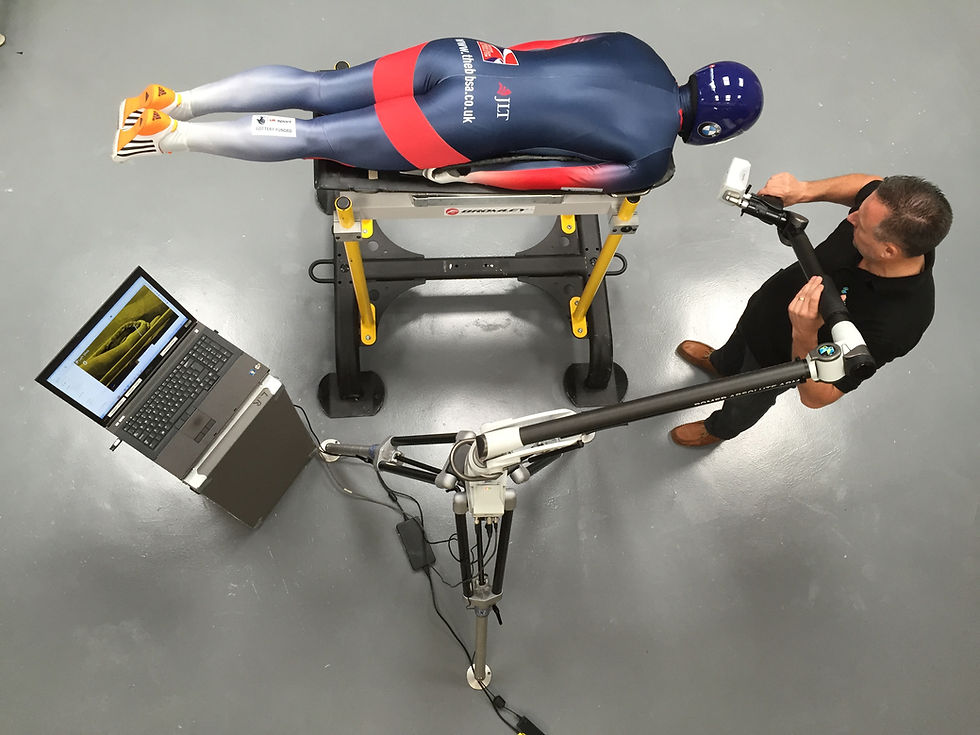
3d Scanning of 2018 Olympic bronze medal winning GBR athlete Dom Parsons on board his Bromley Sports sled. Scanning performed using a Hexagon Absolute Arm

Digital Twin of 2018 Olympic athlete, Alex Hanssen, NOR onboard his Bromley Sports sled
CFD Analysis
Analysis of the athlete aerodynamic system is made using Computational Fluid Dynamics using ANSYS Fluent. This 'virtual wind tunnel' allows changes in drag to be calculated from variations in sled design and other areas of apparel innovation.
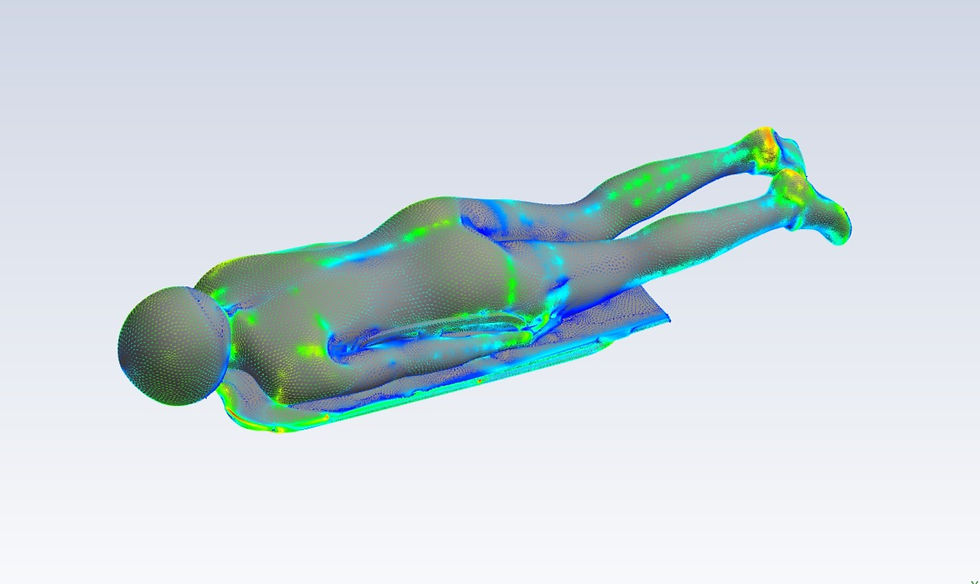
CFD analysis of Olympic bronze medallist Kimberley Bos NED, onboard her Bromley Sports sled, 2022.
Collaboration with CFD Partner EDR Medeso
Wind Tunnel Testing
Validation of CFD results and analysis of more detailed innovations such as suit material and helmets are tested in the Wind tunnel. This final stage of performance analysis compliments the digital twin research phase. This stage includes design and manufacture of attachments and fittings to make the set-up as efficient as possible.

Kimberley Bos NED in the Williams F1 wind tunnel in 2017
We have worked with numerous wind tunnels over the last two decades, building up a unique experience base of experimental wind drag analysis. Wind tunnels we have worked with include: BAESYSTEMS, Brawn F1 (now Mercedes), Williams F1, Glasgow University, Southampton University, Delft Technical University.

Kimberley Bos NED with her bronze Olympic medal Beijing 2022 with Kristan Bromley & Joska le Conte.
Prototype Development
The final stage in the process is developing athlete specific prototypes. The sled development is delivered by Bromley Sports as part of a bespoke athlete performance programme.
Our Partners
Bromley Sports
Williams F1
ANSYS / EDR Medeso
Hexagon Metrology
TU Delft
Commentaires