Thermoformed Structural Composite Part
- kristan209
- Jun 24, 2022
- 2 min read
Updated: Jul 5, 2022
“The sweet spot for composites is the ability to combine key attributes to solve current challenges; #fastcycletimes, #lowerproductioncosts, #lightweighting, #highstiffness, #sustainablematerials, #lowcarbonprocesses , #endoflife options”
Advanced composite materials offer unparalleled credentials when it comes to delivering high strength, high stiffness, low weight parts and structures. A technology that was predominantly the realm of aerospace and F1 motorsport is now filtering into more mainstream markets driven by save energy through light weighting and development of lower cost processing options driven by innovations in materials, processing and automation. The composite industry is growing fast. The choice of fibre and resin systems is evolving just as fast to meet the ever increasing demand for new applications. The move away from expensive autoclave systems and towards lower cost, faster cycle time production solutions is opening up the opportunities around advanced composites to more sectors than ever before.
The Challenge:
To develop a more sustainable , high strength lightweight composite component with complex 3d curved geometry, that can be mass produced at lower cost than traditional materials & processing options.
Key deliverables:
Consider sustainable options.
Develop a material & process combination that can be readily shaped into 3d geometric curved forms.
Include integrated fixture points into the manufacture process.
The choice of production method to yield the required quantities of 100's parts per week from one tooling investment.
Reduce part production costs (Autoclave processing being the baseline).
Sustainability
For this project, sustainability was considered on two fundamental levels:
Processing (energy savings/
Materials
Low processing waste
Design
The key considerations:
Laminate / sandwich construction to meet lightweight/strength requirements
Material form-ability
High volume potential, low manufacture costs
Process
To meet the production volume and cost requirements, compression moulding methods using matched metal tooling in a forming press were chosen. Press forming of composite sandwich structures in a closed metal tool lent itself well to the component geometries being considered.
2. The composite panel was designed using PTC CREO CAD. Working in collaboration with the National Composites Centre NCC (under a Catapult grant award) a structural FEA model of a composite laminate structure was developed using ABACUS. Numerous design iterations and corresponding analysis were undertaken to achieve the desired panel properties.
Fabric drapability analysis was performed using CATIA for feasibility of material forming within the tool geometry.
Materials tested for:
Carbon fibre
Basalt fibre
Glass fibre
Hybrid systems
Various core materials
3. Matched compression mould tools were developed and machined.
4.Compression moulded test panels were produced using our inhouse composite moulding press. A combination of tooling heat and pressure control enabled cycle times under 5 minutes to be achieved.
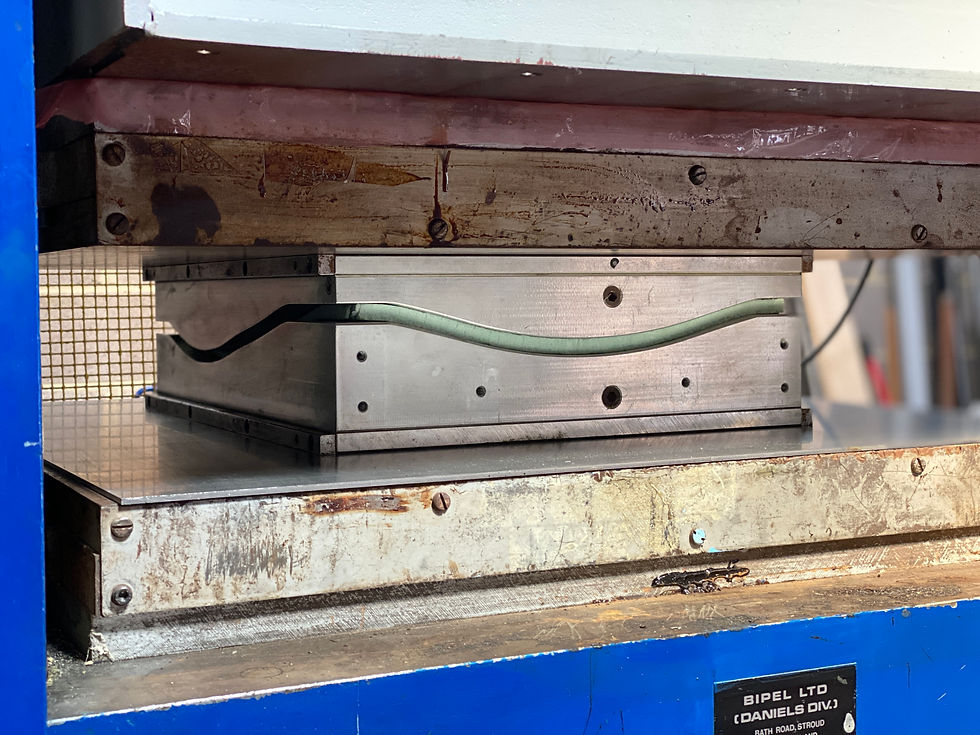


Components were post processed to final geometry using 5 axis CNC trimming including vacuum jig tooling development.
Interested to know
For more detailed information, please contact us directly.
Comments