High Strength, Lightweight Composite Sandwich Panel Component with 3d printed attachments
- kristan209
- Jul 1, 2022
- 2 min read
Updated: Jul 5, 2022
“The sweet spot for composites is the ability to combine key attributes to solve current challenges; #fastcycletimes, #lowerproductioncosts, #lightweighting, #highstiffness, #sustainablematerials, #lowcarbonprocesses , #endoflife options”
The Project
To develop a high strength composite sandwich panel component with high stiffness, fast production times, low cost, using more sustainable materials and processing options.
Requirements:
Achieve a cycle time of less than 5 minutes for board sizes ranging from 0.5m x 05m to 2m x 1m
Robust, crush resistant fixing points at fasteners locations
Bespoke edge trip offering protection and edge finishing
Panel thickness tolerance of 0.5mm
Minimise processing waste e.g. bagging waste
Target sustainable materials/process end of life options
Bespoke edge trimming
Our Solution
We focussed on hot composite moulding processing to achieve the fast cycle time processing targets. Hot compression moulding as a process is considerably less energy demanding than traditional autoclave systems, can achieve low cycle times with the use of snap cure resin systems and achieve significant cost reduction through the reduction of labour costs associated with hand lay up processing.
Using our inhouse hot compression moulding presses, we investigated the use of various reinforcement fibres, core materials & resin systems. In particular the use of snap cure resin systems capable of cure within 2-3 minutes at 150-160C were targeted.
Our KBX Tech in house heat presses are capable of processing materials up to 360C with pressures up to 35 bar, either as flat components or 3d geometries via matched metal tooling.

The following fibre, resin core and processing options were investigated to achieve the set requirements.
Carbon, Kevlar, glass, basalt, flax reinforcements
Balsa, honeycombs, structural foam cores.
Bio resins, including bio-epoxies, PFC
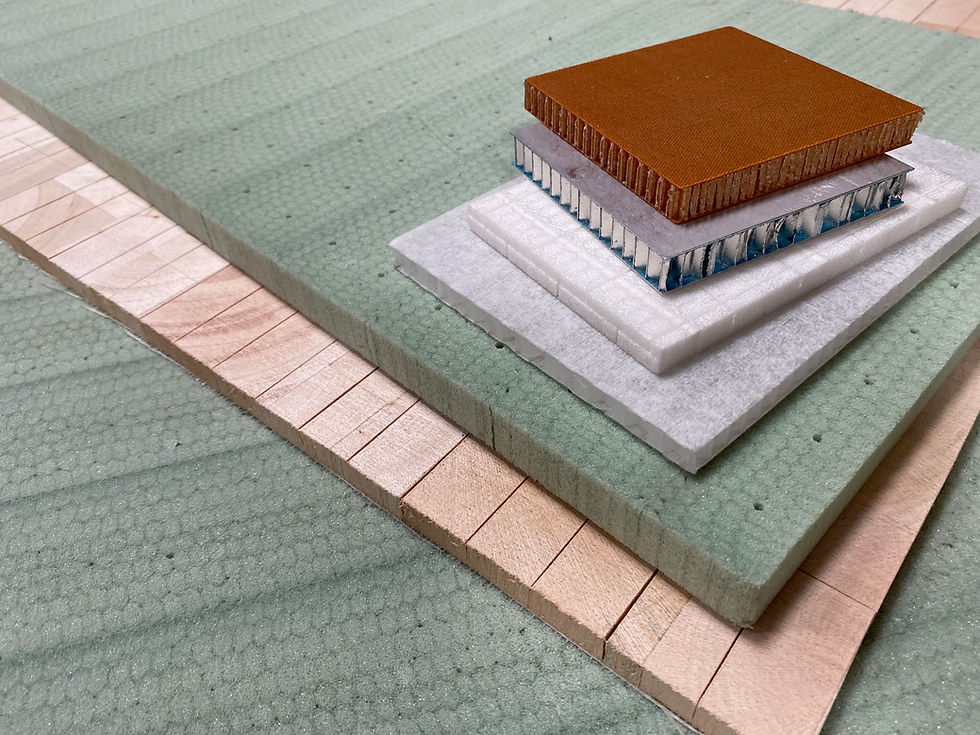
Bepoke 3d printed edge trimming were designed and printed using engineering thermoplastic Onyx on our Markforged 3d printer. These components were developed to support final manufacture using high volume injection moulding.
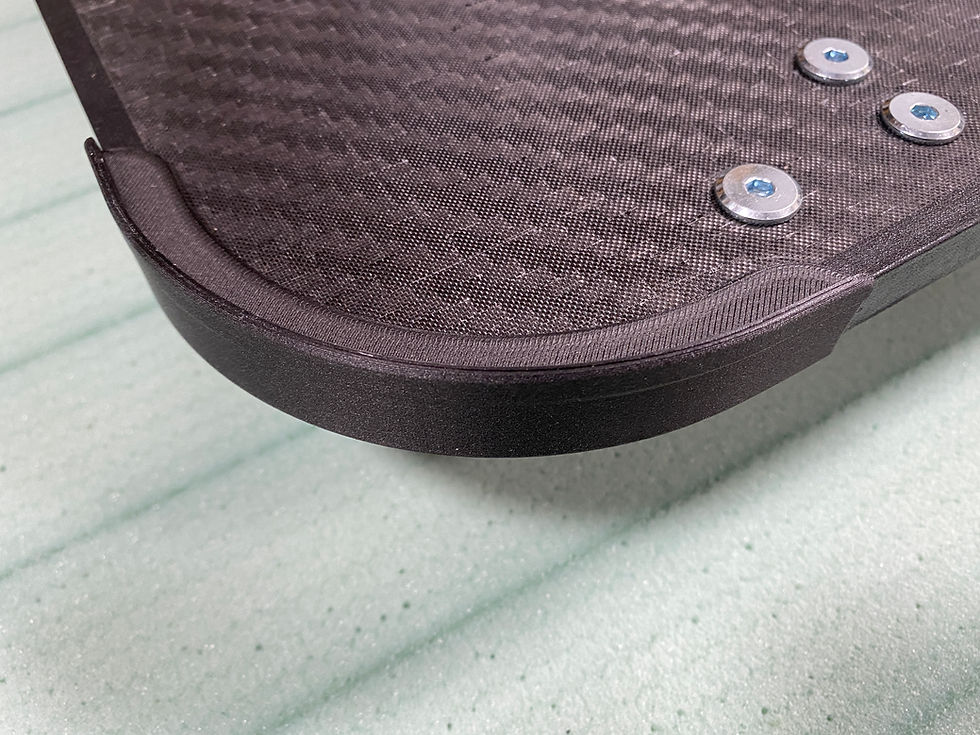
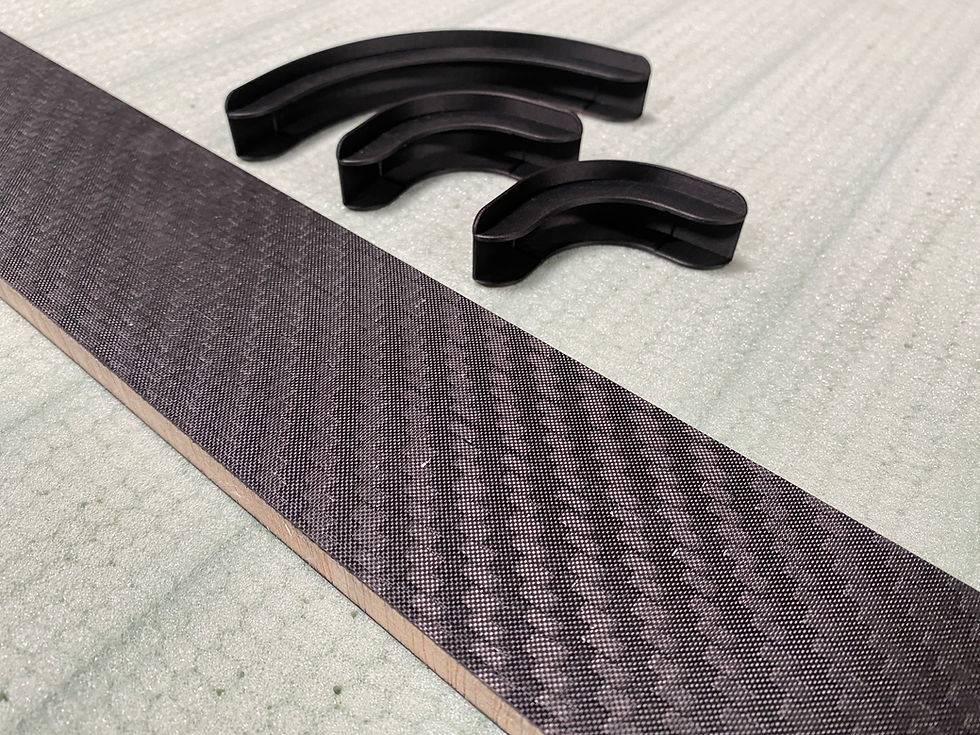
Image: Carbon fibre + Balsa core panel section

Image: Basalt fibre/PFC resin + Balsa core panel

Image: Flax + bio-epoxy resin + Balsa core panel
How can we help?
Interested in developing bespoke compression moulded composite parts?
Contact us to find out how we can help.
Interested in composite sandwich panels?
We are able to supply prototyping through to batch manufacature services with panels ranging in size up to 2mx 1m.
Comments