Development of an Ultra Lightweight, IoT Enabled, Generative Designed, Robotic Arm
- kristan209
- Feb 18, 2022
- 2 min read
Updated: Jul 5, 2022
Challenge:
We were tasked with developing a lightweight robotic arm, actuated with a micro hydraulic system, and controlled / monitored by a remote IoT interface.

Rendered image of the robotic arm design
Rendered video of robotic arm design
Our Solution
A hybrid structure using generative design inspiration and advanced composite materials enabled performance limits to be pushed to teh extreme.
Lightweight Structure
Our solution focused on the use of high performance carbon composite materials & generative design inspired actuator joints to create a ultra #lightweight #robotic #arm structure.
The main structure used a carbon fibre epoxy strengthened tube for it's high strength to weight ratio properties. Tubing geometry was chosen due to it's high torsion & bending stiffness characteristics. Carbon fibre orientation enabled tailored strength properties to suit the specific loading requirement.
The pivot and actuator joints were designed to connect to the ends and body of the carbon tubing respectively. Generative design methods were employed to create an ultra lightweight 3d printable joint design that manages the loading from the hydraulic actuator into the carbon fibre tubes. Titanium was chosen as the printable metal due to it's high strength to weight ratio and low passive corrosion characteristics with carbon fibre.


Facet model of generative designed joint

Facet model of generative designed connector

Surface model of generative designed actuator - tube clamp
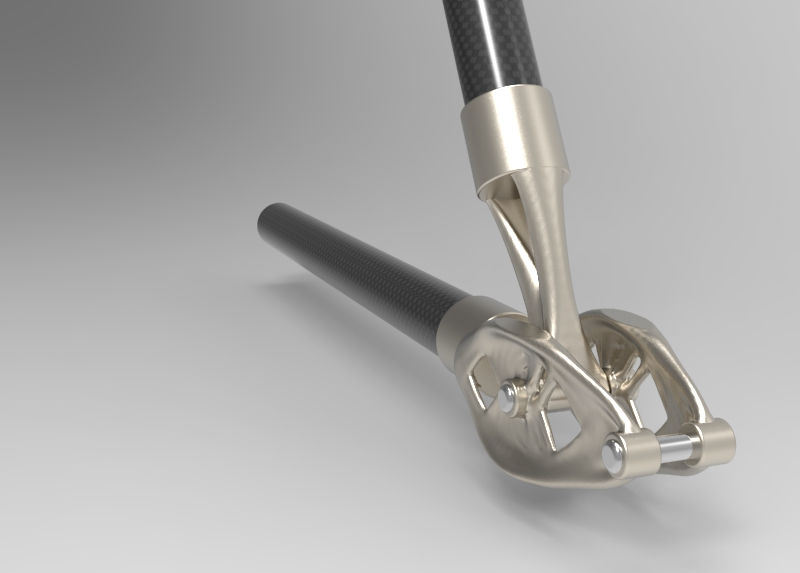
Rendered image of the joint an tube configuration

Rendered image of the arm underside
Micro-hydraulic actuator
The 2-way micro #hydraulic #actuator was developed by MHDE Ltd. The actuator weighing only 250g, was adapted to deliver a specified torque through the linkage. Quick release couplings allowed fast hose disconnection. The anodised aluminium body created an appealing aesthetic finish.
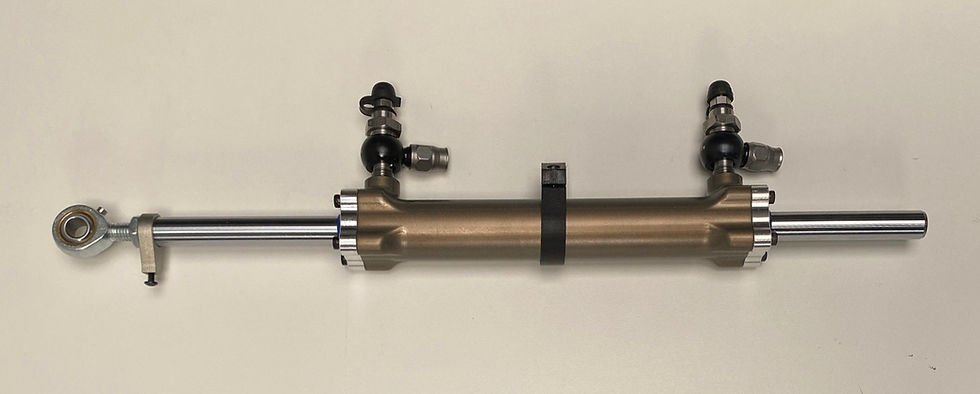
Image of the micro hydraulic ram. This image shows a through rod design option
Valve Control System
Proportional solenoid valves managed the force and speed of #actuator movement with closed loop control. Potentiometers were used for positional feedback. Pressure sensors were used for force feedback and monitoring.
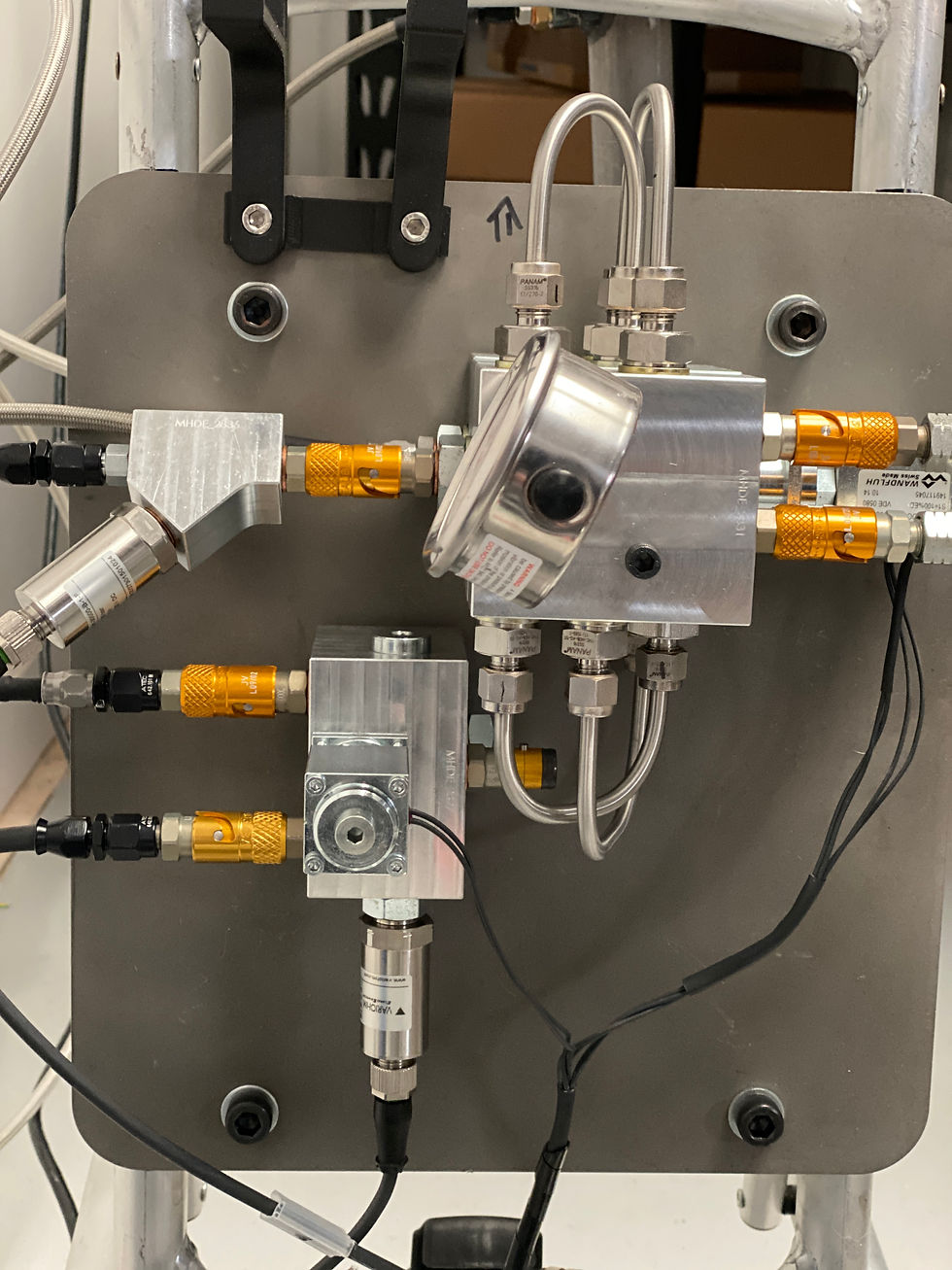
Image of the control valve arrangement

Image of the actuator during testing
IoT Control System
The #robotarm communicated with a #Thingworks #IoTplatform using wifi to allow remote control and monitoring. Local computing power was provided by onboard Arduino systems to manage valve control, sensors and wifi & bluetooth connectivity. Programming languages used: C, C++. Developer tools were written in Java in support of systems testing.
The IoT control system enabled remote control and monitoring of the hydraulic system performance.

Image of the onboard device computing system

Image of the valve electronics control system

Image of the IoT software interface enabling remote monitoring & control of the robot arm device
Dynamometer Test System
A reciprocating #dynamomenter was developed to measure actuator force output, motion monitoring and provide final actuator calibration.
Arduino systems and Java code were developed to control the dynamometer test system.


CAD Image of the bespoke designed dynamometer for actuator calibration and performance measurement
Interested to know more?
Please contact us.
Comentários