Thermal - Fluid Analysis of an Oil Heated Platen
- kristan209
- Feb 23, 2022
- 2 min read
Updated: Jul 7, 2022
“Creating, even and accurate temperature control on platen surfaces is an age old challenge.”
The Challenge
Uneven temperature gradients in heated platens are an age old problem. Processing of materials such as advanced composites require precise control of cure temperatures in order to minimise inherent stress creation during cure, resulting in part war-page and ultimately rejection.
Heating & cooling of metal tooling with fluids with heating & cooling cycles in one closed loop offers an alternative thermal management solution to separate electric cartridge heat and water cooled systems. However achieving even temperature distributions using fluids is problematic primarily due to heat losses from the fluid into the tool as it travels through the tool, resulting is hotter fluid entry and cooler exit zones.
We were tasked with designing a 2m x 1m platen heated and cooled by a hot oil system to create an even temperature distribution with maximum temperature variation across the surface of two degrees.
Our Solution
A Cad design of a 2m x 1m Aluminium platen was developed with integral cooling channels and flow directors.
Fluid / thermal analysis using ANSYS was used to develop a design direction for the platen design, including:
Platen material (steel vs aluminium)
Coolant options (Oil vs water vs Glycol)
Cooling channel spacing & location
Flow baffle design
Platen thickness variation
Inlet / outlet port variation
Pressure differentials & oil flow rate variations
Insulation
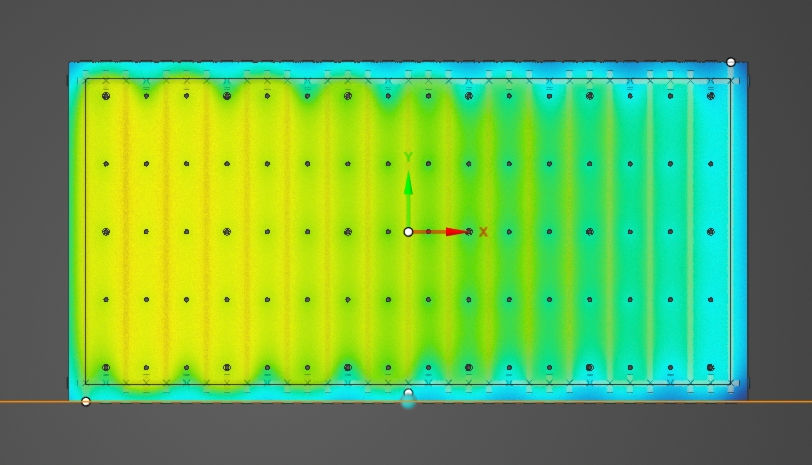
A thermal-fluid analysis of a convention in / out oil flow arrangement in the platen design was undertaken.
Parameter sweeps were set up to create fast analysis of design variables, reducing analysis time/cost. This early stage analysis enabled a fast sensitivity based assessment of thermal response in the platen to varying the variable conditions.
ANSYS simulation of the fluid-thermal results
High fidelity analysis was then performed on the final design / variable configuration, including development of a manifold design for oil distribution from the oil heater to the platen.
Through fine tuning of design parameters and focussing in on key variables, a platen temperature variation of 2x1m platen surface of one degree Celsius was achieved,
A final platen design was completed.
Manufacture
Two 2x1m precision platens were manufactured with gun drilled cooling channel arrays. CNC fixing point were machined into the tooling surface.

KBX Tech manged the whole project from background research, concept design, analysis, manufacture project management, test.
Do you have a thermal, fluid or multi physics challenge?
Why not contact us to see how we can help!
Comentários